프로젝트 개요
1. 제작 프로그램
600세트/일(117/118 베어링 받침대)
2. 가공 라인에 대한 요구 사항:
1) 자동 생산라인에 적합한 NC 가공센터;
2) 유압식 프록 클램프;
3) 자동적재 및 블랭킹 장치와 운반장치;
4) 전반적인 처리 기술 및 처리 주기 시간;
생산 라인의 레이아웃
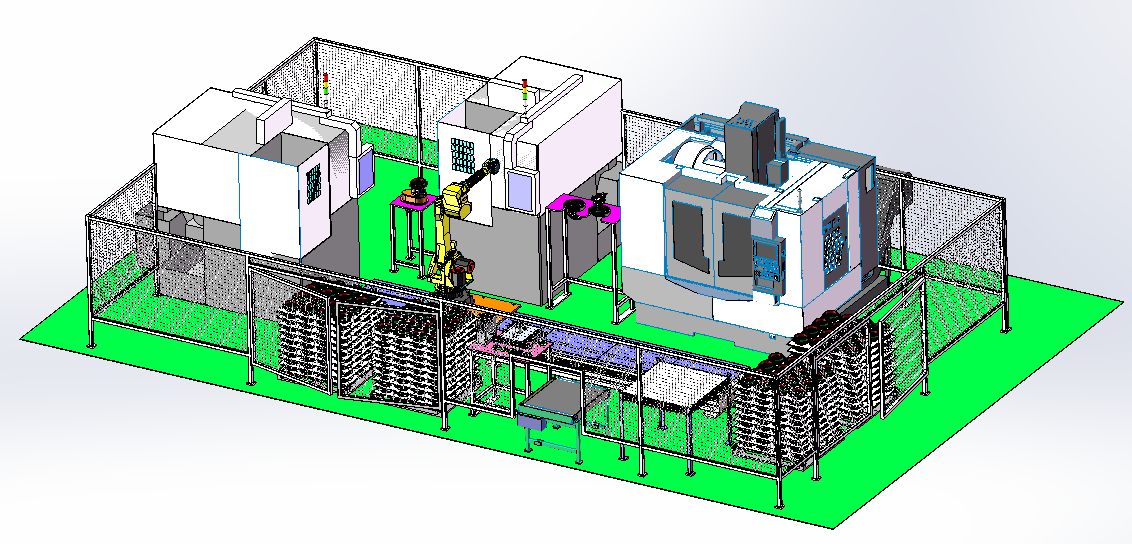
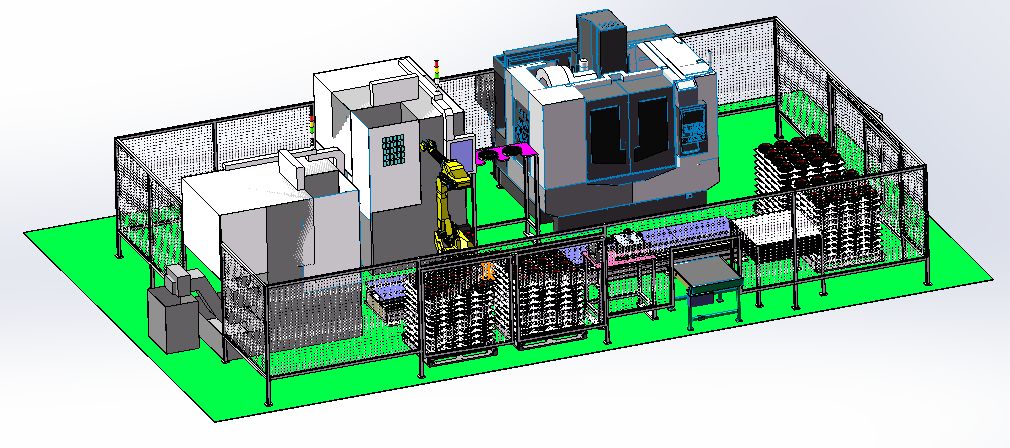
생산 라인의 레이아웃
로봇 액션 소개:
1. 대략 가공하여 배치한 바구니를 수동으로 로딩 테이블(로딩 테이블 No. 1 및 No. 2)에 올려놓고 버튼을 눌러 확인합니다.
2. 로봇은 1번 적재 테이블의 트레이로 이동하여 비전 시스템을 열고 부품 A와 B를 각각 잡아 각도별 관찰 스테이션으로 옮겨 적재 지시를 기다립니다.
3. 각도 인식 스테이션에서 적재 명령이 전송됩니다. 로봇은 1번 조각을 턴테이블의 위치 지정 영역에 놓습니다. 턴테이블을 회전시키고 각도 인식 시스템을 작동시켜 각도 위치를 확인한 후, 턴테이블을 정지시키고 1번 조각의 각도 인식을 완료합니다.
4. 각도 인식 시스템이 블랭킹 명령을 전송하고, 로봇은 1번 조각을 집어 들고 2번 조각을 식별을 위해 넣습니다. 턴테이블이 회전하고 각도 인식 시스템이 작동하여 각도 위치를 확인합니다. 턴테이블이 멈추고 2번 조각의 각도 인식이 완료되면 블랭킹 명령이 전송됩니다.
5. 로봇은 1번 수직 선반의 블랭킹 명령을 수신하여 1번 수직 선반의 소재 블랭킹 및 적재 위치로 이동합니다. 작업이 완료되면 수직 선반의 단일 부품 가공 사이클이 시작됩니다.
6. 로봇은 1번 수직 선반으로 완제품을 가져와서 작업물 롤오버 테이블의 1번 위치에 놓습니다.
7. 로봇은 2번 수직 선반의 블랭킹 명령을 받고, 2번 수직 선반의 로딩 및 블랭킹 위치로 이동하여 소재 블랭킹 및 로딩을 수행한 후 작업이 완료되고 수직 선반의 일체형 가공 사이클이 시작됩니다.
8. 로봇은 2번 수직 선반으로 완제품을 가져와서 작업물 롤오버 테이블의 2번 위치에 놓습니다.
9. 로봇은 수직 가공에서 블랭킹 명령을 기다립니다.
10. 수직 가공에서 블랭킹 명령을 전송하면 로봇이 수직 가공의 로딩 및 블랭킹 위치로 이동하여 1번 및 2번 스테이션의 공작물을 각각 블랭킹 트레이로 잡아 이동시키고, 공작물을 각각 트레이에 놓습니다. 로봇이 롤오버 테이블로 이동하여 1번 및 2번 공작물을 각각 잡고 수직 가공 로딩 및 블랭킹 위치로 보내고, 1번 및 2번 공작물을 각각 유압 클램프의 1번 및 2번 스테이션 위치 지정 영역에 놓아 수직 가공 로딩을 완료합니다. 로봇이 수직 가공의 안전 거리를 벗어나 단일 가공 사이클을 시작합니다.
11. 로봇은 1번 로딩 트레이로 이동하여 2차 사이클 프로그램의 시작을 준비합니다.
설명:
1. 로봇이 로딩 트레이에 16개(한 겹)의 물건을 올립니다. 로봇은 흡착 집게를 교체하고, 분리판을 임시 보관 바구니에 넣습니다.
2. 로봇은 블랭킹 트레이에 16개(한 겹)의 부품을 포장합니다. 로봇은 흡착판을 한 번 교체하고, 임시 보관 바구니에서 나온 부품의 칸막이 면에 칸막이판을 올려놓습니다.
3. 검사 빈도에 따라 로봇이 부품을 수동 샘플링 테이블에 올려놓도록 합니다.
1 | 가공 사이클 시간표 | ||||||||||||||
2 | 고객 | 공작물 소재 | QT450-10-GB/T1348 | 공작기계 모델 | 보관번호 | ||||||||||
3 | 제품명 | 117 베어링 시트 | 도면 번호 | DZ90129320117 | 준비 날짜 | 2020.01.04 | 준비한 사람 | ||||||||
4 | 프로세스 단계 | 칼 번호 | 가공 콘텐츠 | 도구 이름 | 절단 직경 | 절삭 속도 | 회전 속도 | 회전당 피드 | 공작기계로 공급 | 절단 횟수 | 각 프로세스 | 가공 시간 | 유휴 시간 | 4축 회전 시간 | 공구 교환 시간 |
5 | 아니요. | 아니요. | 설명 | 도구 | 디 mm | n | 오후 12시 | mm/회전 | mm/분 | 타임스 | mm | 비서 | 비서 | 비서 | |
6 | ![]() | ||||||||||||||
7 | 1 | 티01 | 밀링 장착 구멍 표면 | 40면 밀링 커터의 직경 | 40.00 | 180 | 1433 | 1.00 | 1433 | 8 | 40.0 | 13시 40분 | 8 | 4 | |
8 | DIA 17 장착 구멍 드릴 | DIA 17 복합 드릴 | 오후 5시 | 100 | 1873 | 0.25 | 468 | 8 | 32.0 | 32.80 | 8 | 4 | |||
9 | T03 | DIA 17홀 백 챔퍼링 | 역방향 챔퍼링 커터 | 16.00 | 150 | 2986 | 0.30 | 896 | 8 | 30.0 | 16.08 | 16 | 4 | ||
10 | 설명: | 절단 시간: | 62 | 두번째 | 고정장치를 사용한 클램핑 및 재료 로딩 및 블랭킹 시간: | 30.00 | 두번째 | ||||||||
11 | 보조 시간: | 44 | 두번째 | 총 가공 인력 시간: | 136.27 | 두번째 |
1 | 가공 사이클 시간표 | |||||||||||||||||
2 | 고객 | 공작물 소재 | QT450-10-GB/T1348 | 공작기계 모델 | 보관번호 | |||||||||||||
3 | 제품명 | 118 베어링 시트 | 도면 번호 | DZ90129320118 | 준비 날짜 | 2020.01.04 | 준비한 사람 | |||||||||||
4 | 프로세스 단계 | 칼 번호 | 가공 콘텐츠 | 도구 이름 | 절단 직경 | 절삭 속도 | 회전 속도 | 회전당 피드 | 공작기계로 공급하다 | 절단 횟수 | 각 프로세스 | 가공 시간 | 유휴 시간 | 4축 회전 시간 | 공구 교환 시간 | |||
5 | 아니요. | 아니요. | 설명 | 도구 | 디 mm | n | 오후 12시 | mm/회전 | mm/분 | 타임스 | mm | 비서 | 비서 | 비서 | ||||
6 | ![]() | |||||||||||||||||
7 | 1 | 티01 | 밀링 장착 구멍 표면 | 40면 밀링 커터의 직경 | 40.00 | 180 | 1433 | 1.00 | 1433 | 8 | 40.0 | 13시 40분 | 8 | 4 | ||||
8 | T02 | DIA 17 장착 구멍 드릴 | DIA 17 복합 드릴 | 오후 5시 | 100 | 1873 | 0.25 | 468 | 8 | 32.0 | 32.80 | 8 | 4 | |||||
9 | T03 | DIA 17홀 백 챔퍼링 | 역방향 챔퍼링 커터 | 16.00 | 150 | 2986 | 0.30 | 896 | 8 | 30.0 | 16.08 | 16 | 4 | |||||
10 | 설명: | 절단 시간: | 62 | 두번째 | 고정장치를 사용한 클램핑 및 재료 로딩 및 블랭킹 시간: | 30.00 | 두번째 | |||||||||||
11 | 보조 시간: | 44 | 두번째 | 총 가공 인력 시간: | 136.27 | 두번째 | ||||||||||||
12 |
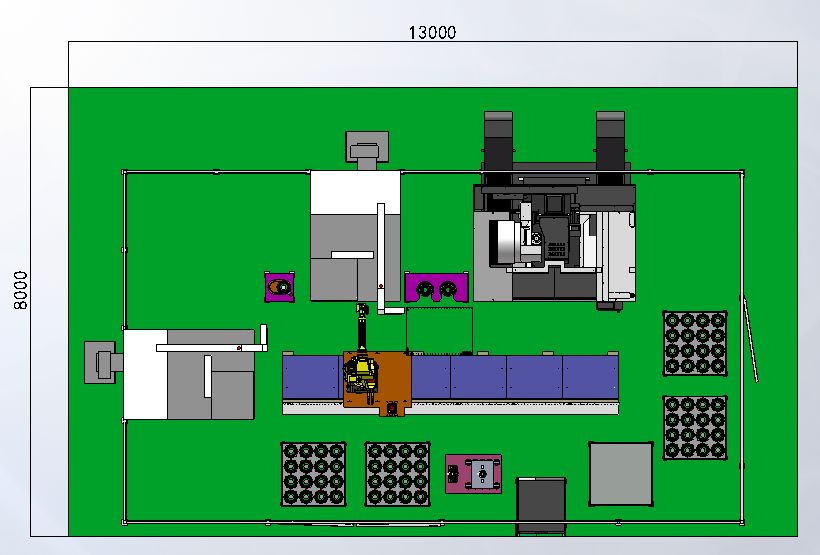
생산라인의 적용범위
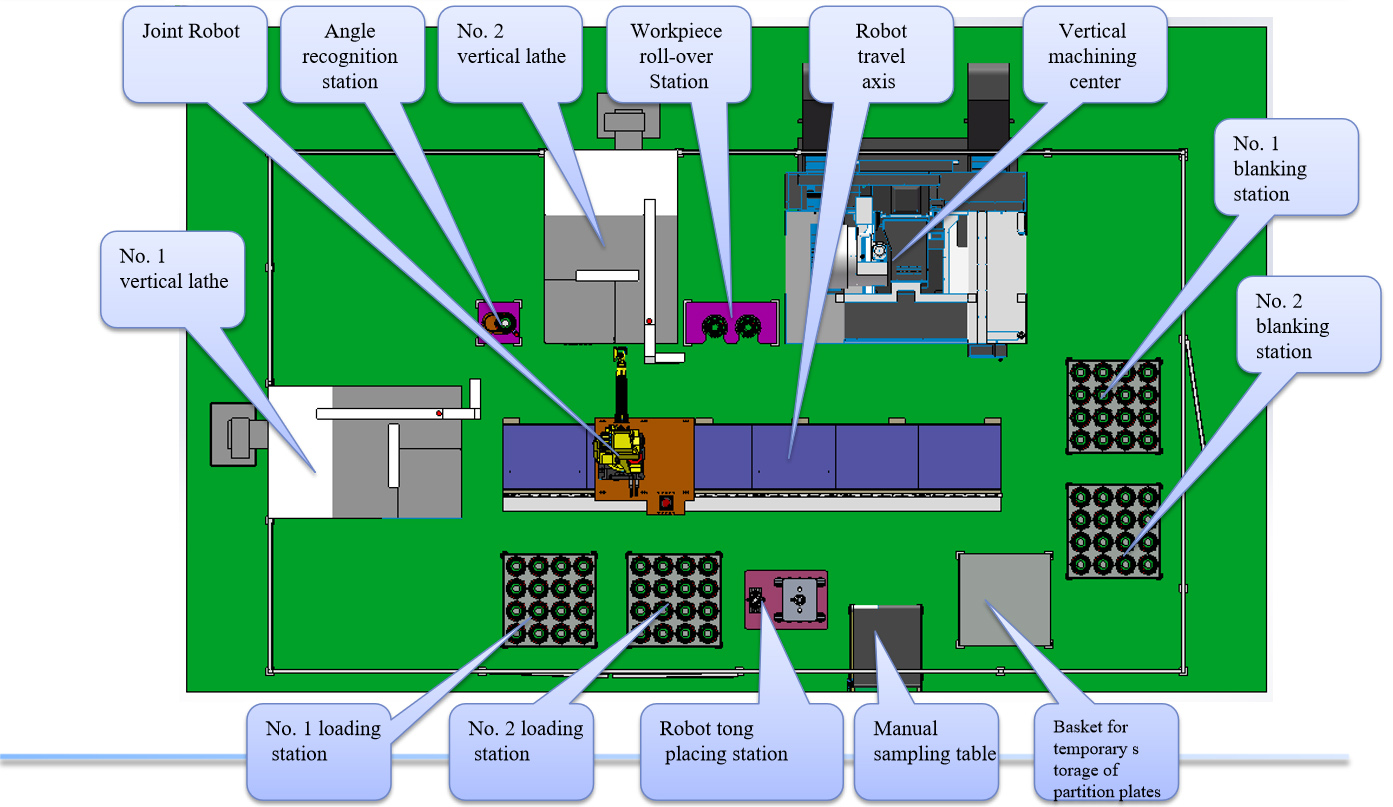
생산라인의 주요 기능 구성 요소 소개
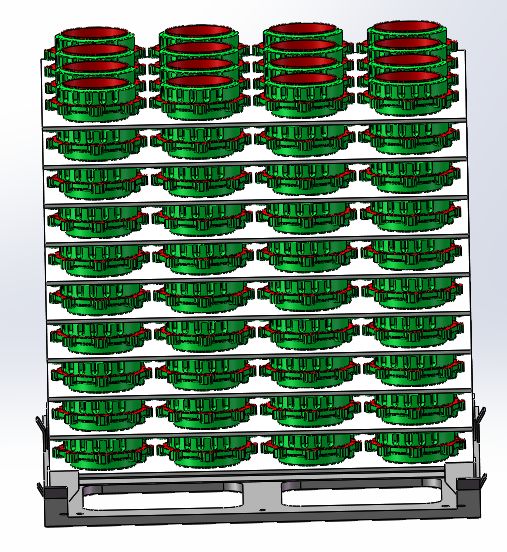
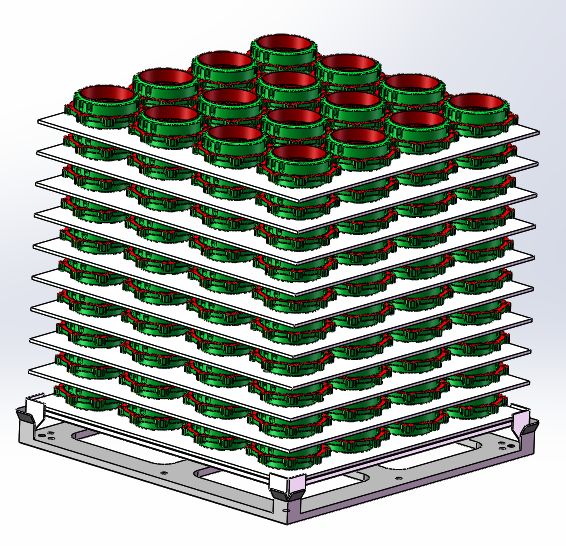
로딩 및 블랭킹 시스템 소개
이 방식에서 자동 생산 라인의 보관 장비는 다음과 같습니다. 쌓인 트레이(각 트레이에 포장할 부품 수량은 고객과 협의해야 함)와 트레이에 있는 작업물의 위치는 작업물 블랭크 또는 실제 물체의 3D 도면을 제공한 후 결정해야 합니다.
1. 작업자는 대략 가공된 부품을 재료 트레이에 포장하고(그림 참조) 지정된 위치까지 포크리프트로 운반합니다.
2. 지게차의 트레이를 다시 장착한 후, 수동으로 버튼을 눌러 확인하세요.
3. 로봇이 작업물을 잡고 로딩 작업을 수행합니다.
로봇 이동축 소개
이 구조는 관절 로봇, 서보 모터 드라이브, 피니언 및 랙 드라이브로 구성되어 로봇이 앞뒤로 직선 운동을 할 수 있도록 합니다. 하나의 로봇으로 여러 공작기계를 지원하고 여러 스테이션에서 공작물을 파지하는 기능을 구현하여 관절 로봇의 작업 범위를 넓힐 수 있습니다.
주행궤도는 강관으로 용접된 베이스를 적용하고 서보 모터, 피니언 및 랙 드라이브로 구동하여 관절 로봇의 작업 범위를 늘리고 로봇의 활용률을 효과적으로 향상시킵니다. 주행궤도는 지면에 설치됩니다.
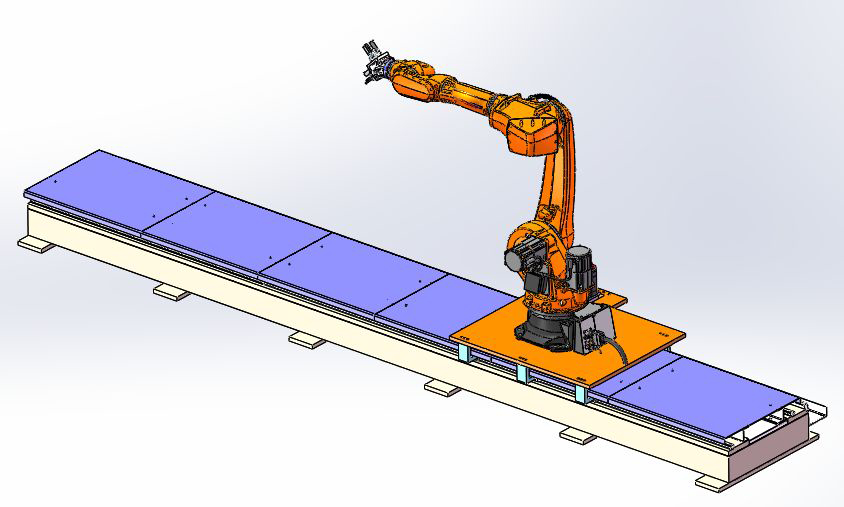
Chenxuan 로봇:SDCX-RB500
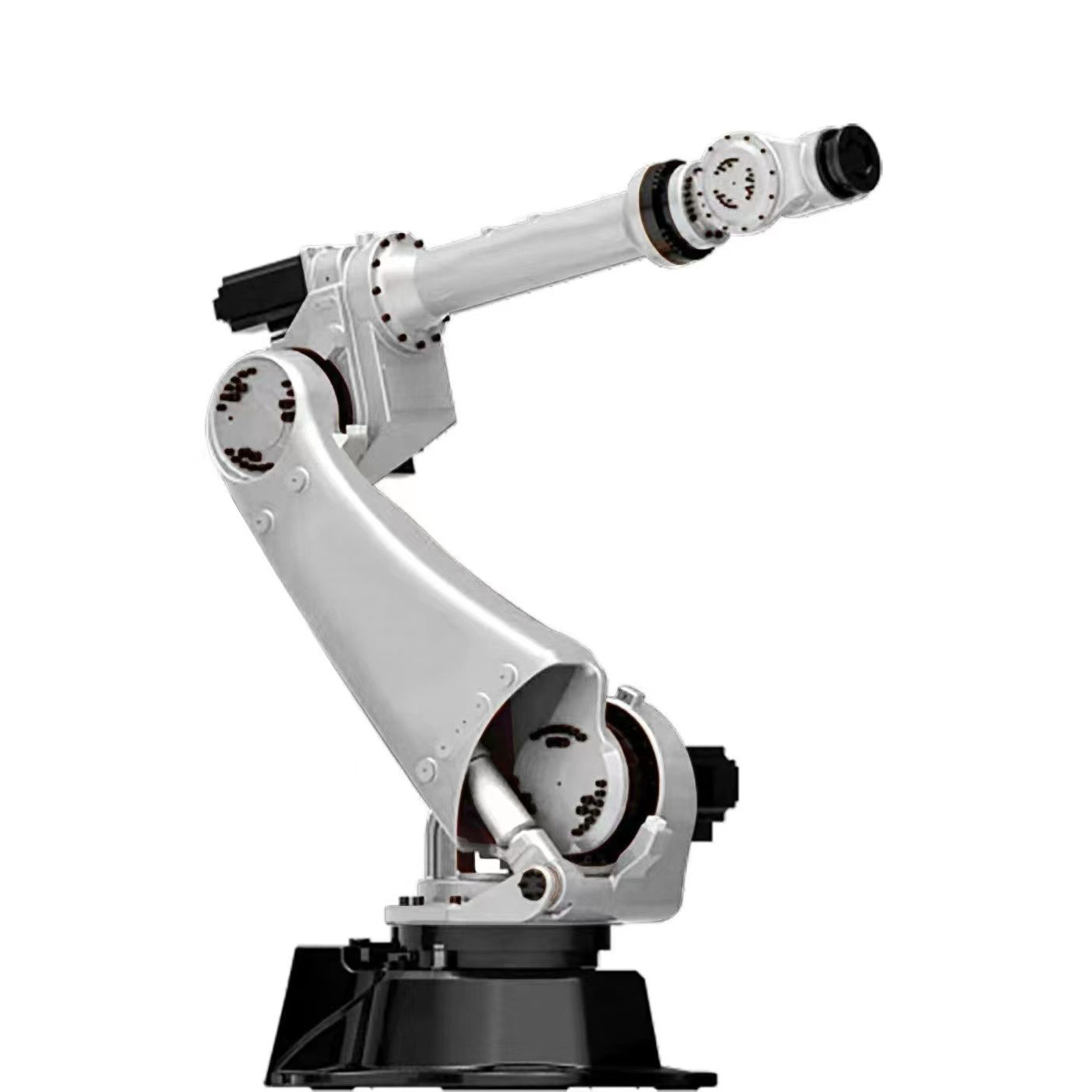
기본 데이터 | |
유형 | SDCX-RB500 |
축의 수 | 6 |
최대 범위 | 2101mm |
포즈 반복성(ISO 9283) | ±0.05mm |
무게 | 553kg |
로봇의 보호 분류 | 보호 등급, IP65 / IP67인라인 손목(IEC 60529) |
장착 위치 | 천장, 허용 경사각 ≤ 0º |
표면 마감, 도장 | 베이스 프레임: 검정색(RAL 9005) |
주변 온도 | |
작업 | 283K ~ 328K(0°C ~ +55°C) |
보관 및 운송 | 233K ~ 333K(-40°C ~ +60°C) |
로봇 후면과 하단에 넓은 동작 영역을 제공하여 천장 리프팅이 가능한 모델입니다. 로봇의 측면 폭이 최소화되어 인접 로봇, 클램프 또는 작업물에 밀착 설치가 가능합니다. 대기 위치에서 작업 위치로의 고속 이동과 단거리 이동 시 빠른 위치 결정이 가능합니다.
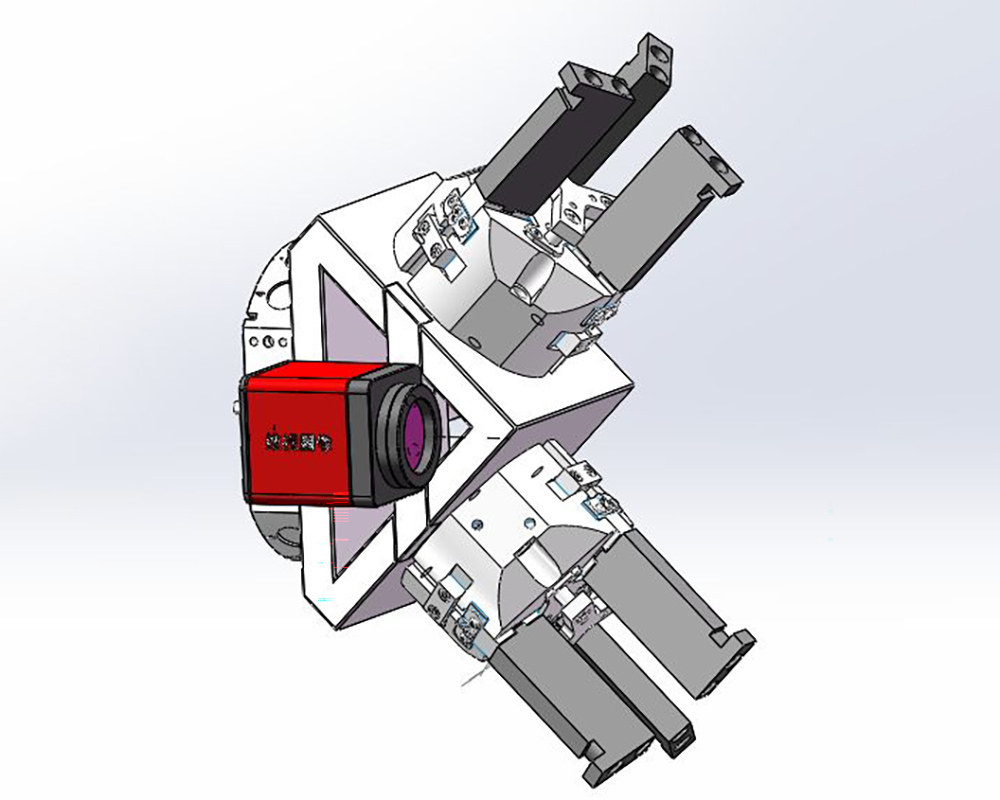
지능형 로봇 로딩 및 블랭킹 통 메커니즘
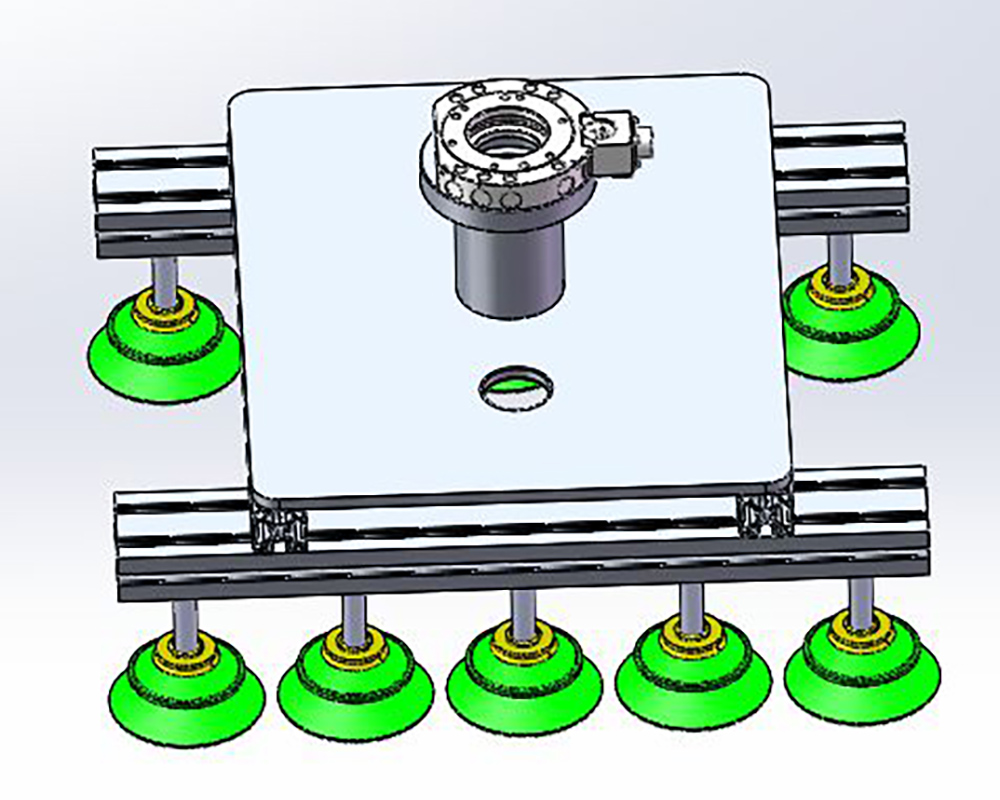
로봇 분할판 집게 메커니즘
설명:
1. 이 부품의 특징을 고려하여 3개의 발톱 외부 지지 방식을 사용하여 소재를 적재하고 블랭킹함으로써 공작 기계에서 부품의 빠른 회전을 실현할 수 있습니다.
2. 본 기구에는 위치 검출 센서와 압력 센서가 장착되어 있어 부품의 클램핑 상태와 압력이 정상적인지 여부를 검출합니다.
3. 본 기계에는 가압기가 장착되어 있어, 정전 및 주공기 회로의 가스 차단 시에도 단시간 내에 공작물이 떨어지지 않습니다.
4. 수동식 교체 장치를 채택했습니다. 집게 교체 메커니즘으로 다양한 소재의 클램핑을 빠르게 완료할 수 있습니다.
통 체인징 장치 소개
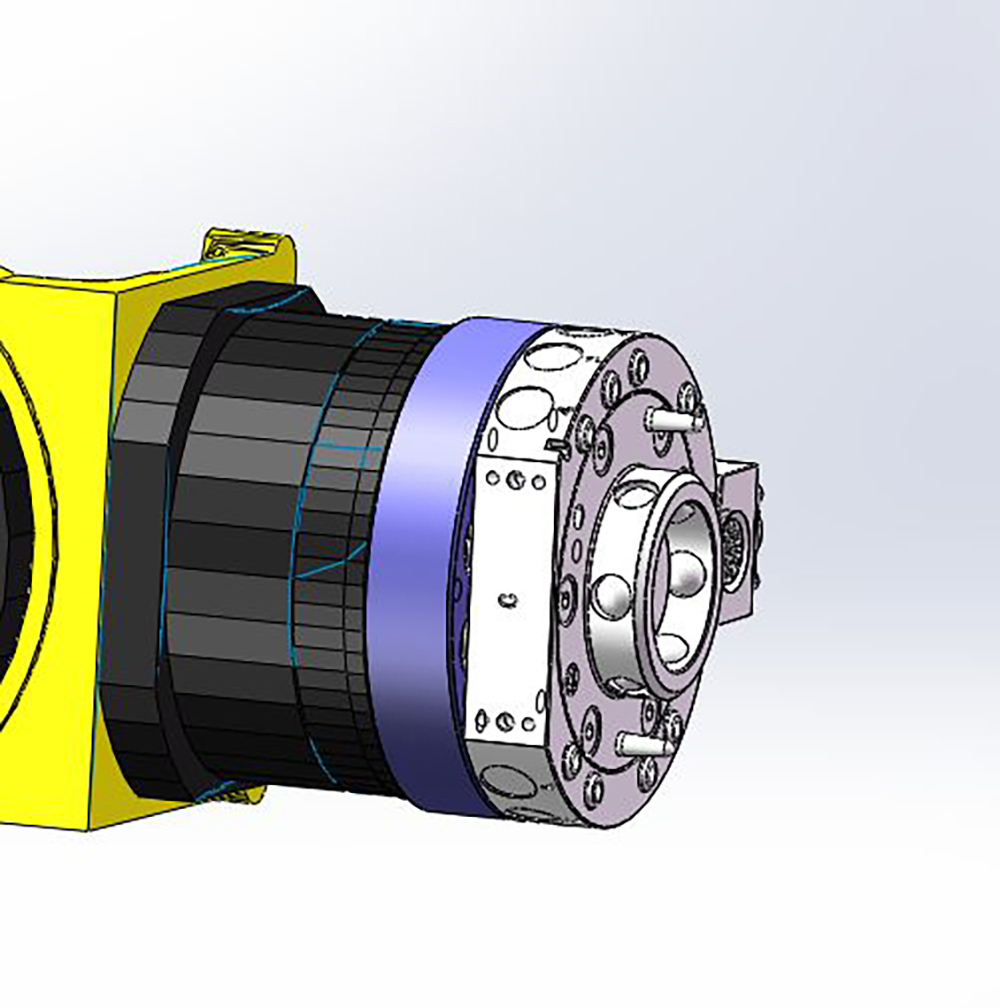
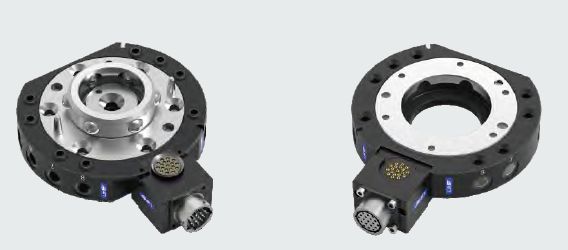
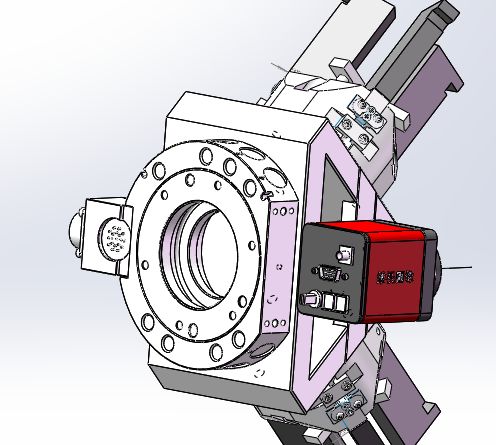
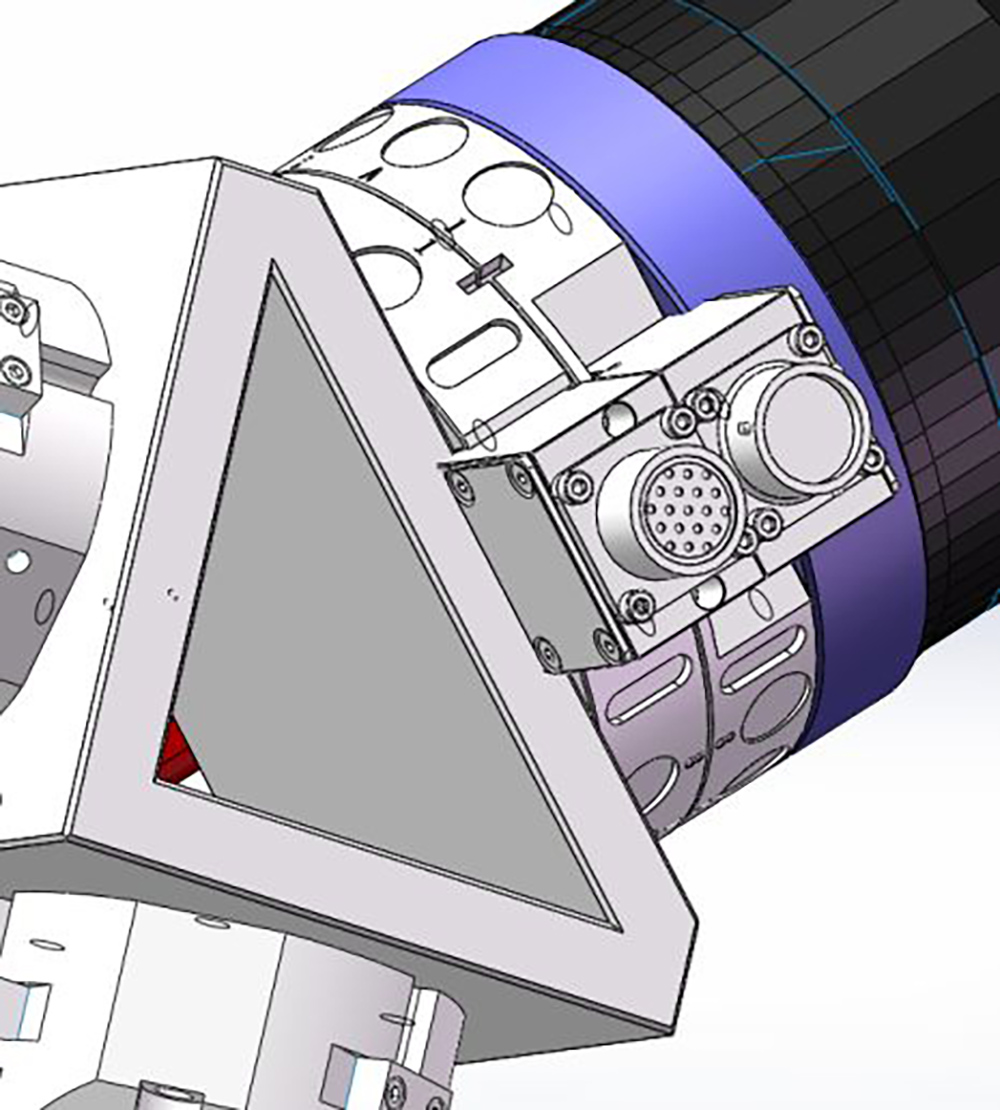
정밀 집게 교체 장치는 로봇 집게, 툴 엔드 및 기타 액추에이터를 신속하게 교체하는 데 사용됩니다. 생산 유휴 시간을 줄이고 로봇 유연성을 향상시키며, 다음과 같은 특징이 있습니다.
1. 공기압을 풀고 조입니다.
2. 다양한 전력, 액체 및 가스 모듈을 사용할 수 있습니다.
3. 표준 구성으로 공기원과 빠르게 연결 가능
4. 특수보험 대행사는 우발적인 가스 차단 위험을 예방할 수 있습니다.
5. 스프링 반력 없음; 6. 자동화 분야에 적용 가능;
비전 시스템 소개 - 산업용 카메라
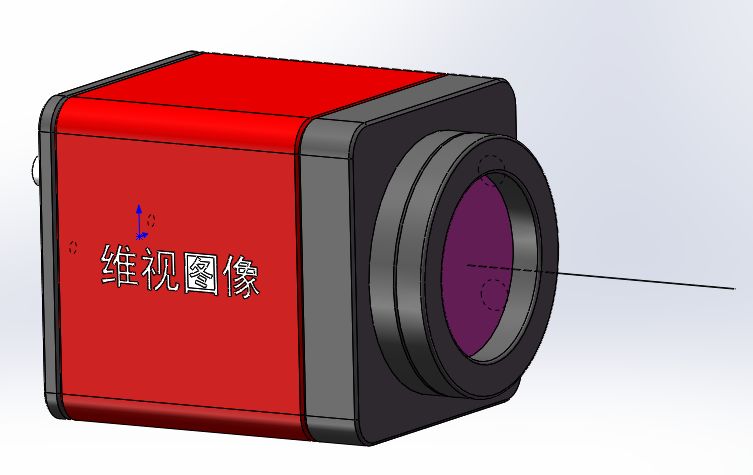
1. 카메라는 고품질 CCD와 CMDS 칩을 채택하여 고해상도, 고감도, 높은 신호 대 주파수 비율, 넓은 동적 범위, 우수한 영상 품질 및 일류 색상 복원 기능의 특징을 가지고 있습니다.
2. 에어리어 어레이 카메라는 GIGabit Ethernet(GigE) 인터페이스와 USB3.0 인터페이스의 두 가지 데이터 전송 모드를 가지고 있습니다.
3. 이 카메라는 콤팩트한 구조, 작은 외관, 가벼운 무게로 설치가 간편합니다. 빠른 전송 속도, 강력한 간섭 방지 기능, 안정적인 고품질 이미지 출력을 자랑합니다. 코드 판독, 결함 감지, DCR 및 패턴 인식에 적합합니다. 컬러 카메라는 강력한 색상 복원 기능을 갖추고 있어 색상 인식 요구 사항이 높은 환경에 적합합니다.
각도 자동 인식 시스템 소개
기능 소개
1. 로봇은 로딩 바구니에서 작업물을 고정하여 턴테이블의 위치 지정 영역으로 보냅니다.
2. 턴테이블은 서보 모터의 구동에 따라 회전합니다.
3. 시각 시스템(산업용 카메라)은 각도 위치를 식별하고, 턴테이블은 필요한 각도 위치를 결정하기 위해 멈춥니다.
4. 로봇이 작업물을 꺼내고 각도 식별을 위해 다른 작업물을 넣습니다.
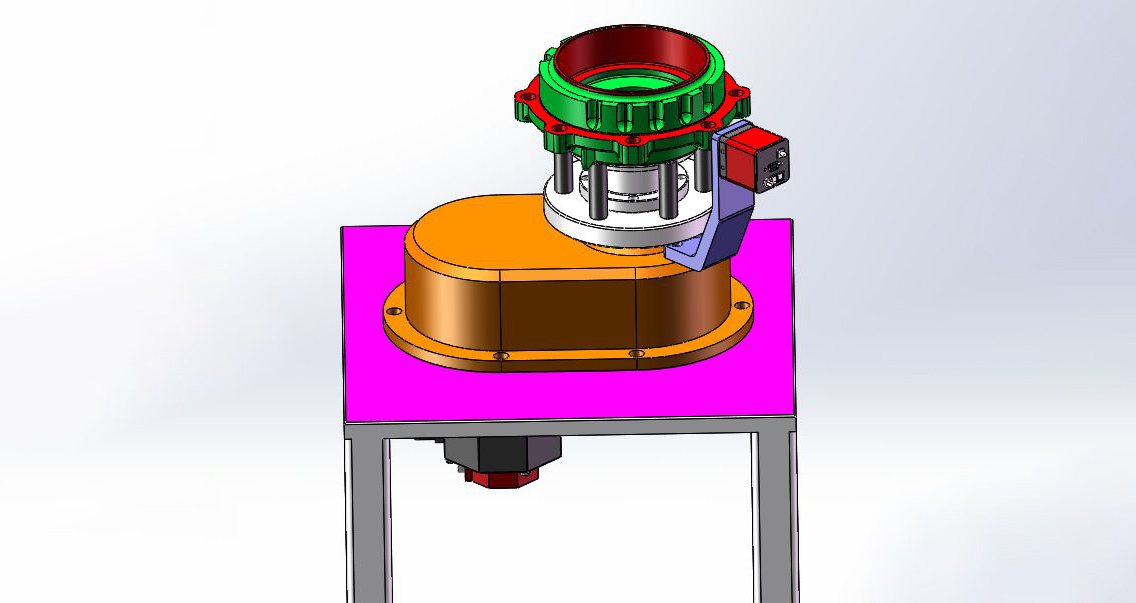
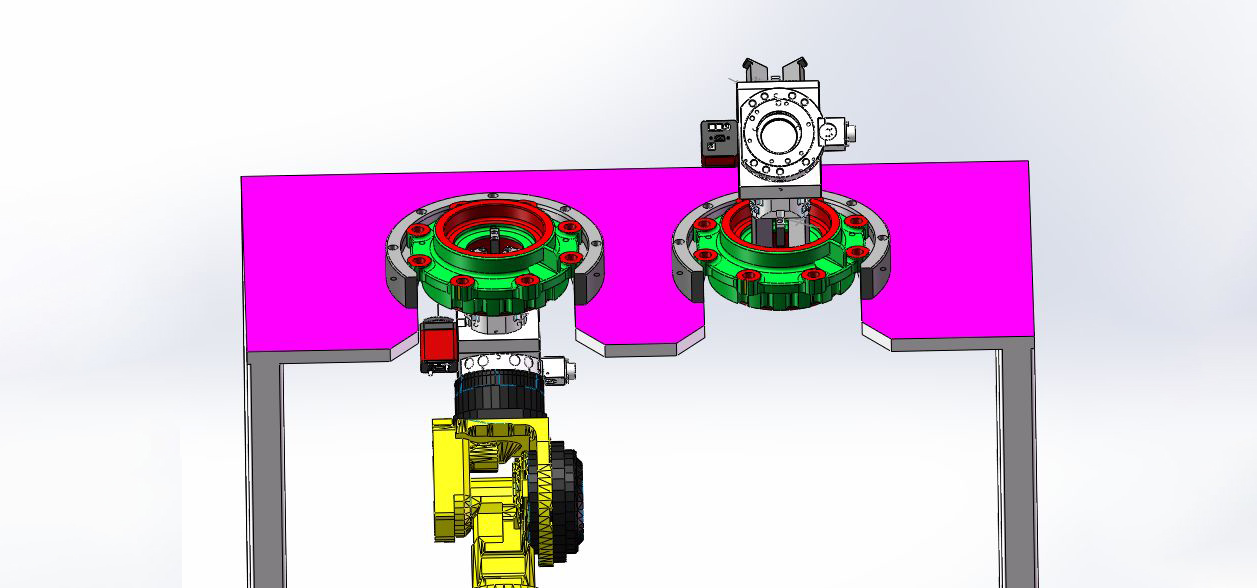
워크피스 롤오버 테이블 소개
롤오버 스테이션:
1. 로봇은 작업물을 가져와 롤오버 테이블의 위치 지정 영역(그림의 왼쪽 스테이션)에 놓습니다.
2. 로봇은 위쪽에서 작업물을 잡아 작업물의 굴림을 실현합니다.
로봇 집게 배치 테이블
기능 소개
1. 각 층의 부품을 적재한 후, 겹겹이 쌓인 분할판을 분할판 임시 보관 바구니에 넣어야 합니다.
2. 로봇은 집게 교체 장치를 통해 흡입 컵 집게로 빠르게 교체할 수 있으며, 칸막이 판을 제거할 수 있습니다.
3. 분할판을 잘 놓은 후 흡입컵 집게를 떼어내고 공압 집게로 교체하여 재료 적재 및 블랭킹 작업을 계속합니다.
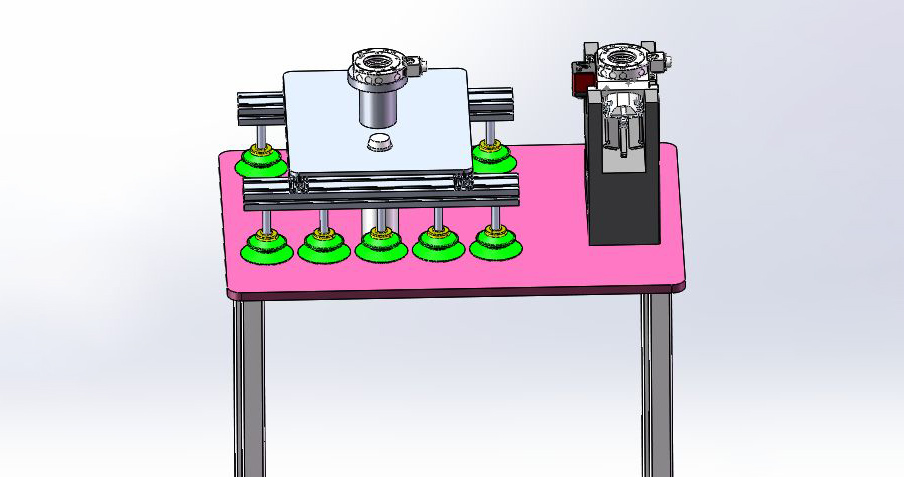
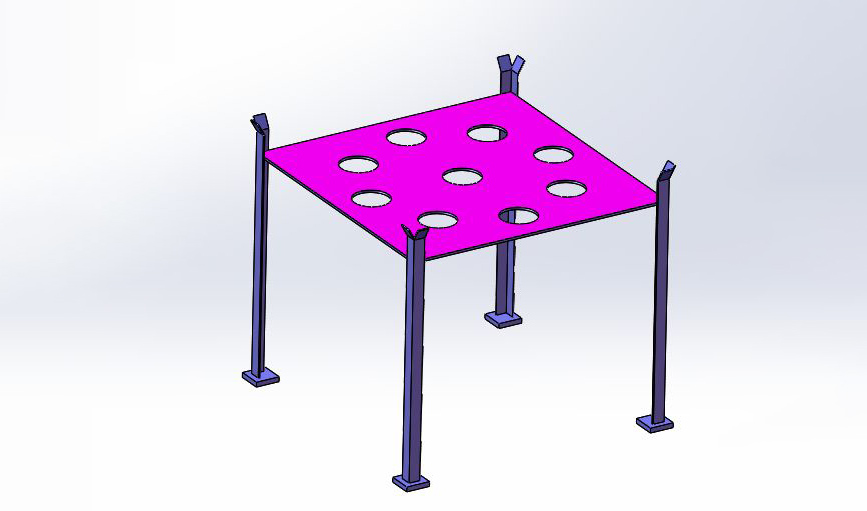
칸막이판 임시 보관용 바구니
기능 소개
1. 적재용 분할판을 먼저 인출하고, 블랭킹용 분할판을 나중에 사용하기 위해 분할판을 위한 임시 바구니를 설계하고 계획합니다.
2. 적재 칸막이판이 수동으로 배치되어 있어 균일성이 떨어집니다. 칸막이판을 임시 보관 바구니에 넣은 후 로봇이 꺼내서 깔끔하게 정리할 수 있습니다.
수동 샘플링 테이블
설명:
1. 다양한 생산 단계에 대해 서로 다른 수동 무작위 샘플링 빈도를 설정하여 온라인 측정의 효과를 효과적으로 감독할 수 있습니다.
2. 사용 설명서: 조작기는 수동으로 설정한 주파수에 따라 작업물을 샘플링 테이블의 설정 위치에 놓고, 빨간색 표시등으로 알려줍니다. 검사자는 버튼을 눌러 작업물을 보호 구역 외부의 안전 구역으로 운반하고, 측정을 위해 작업물을 꺼내 측정 후 별도로 보관합니다.
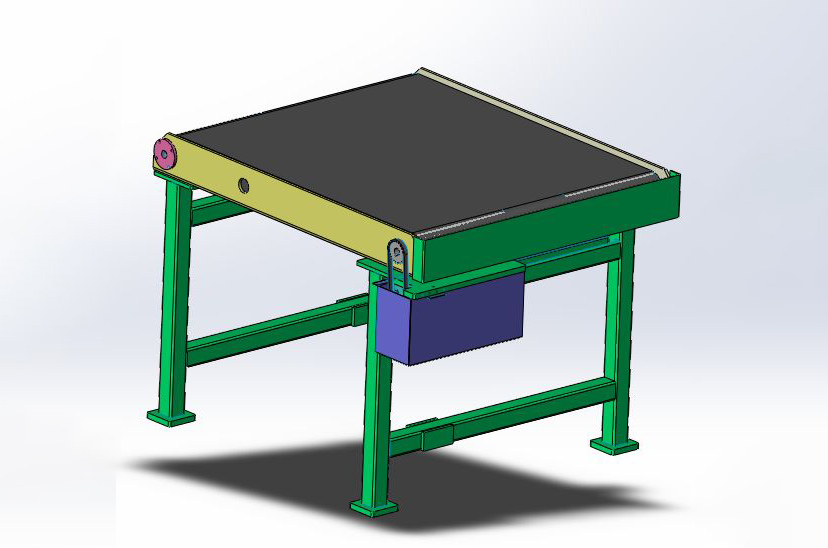
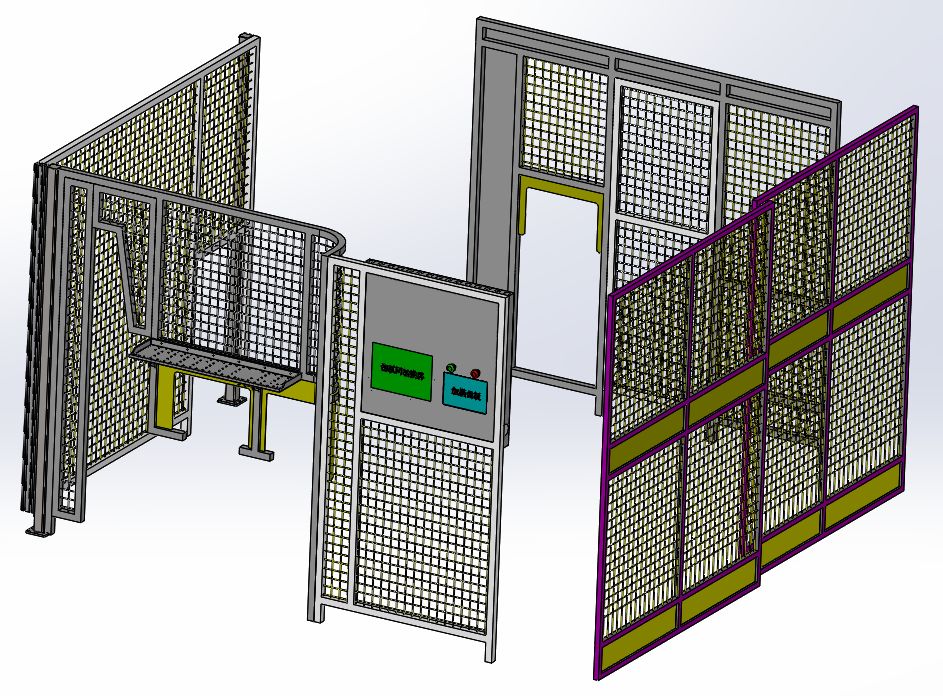
보호 구성 요소
가벼운 알루미늄 프로파일(40×40)+메쉬(50×50)로 구성되었으며, 터치스크린과 비상 정지 버튼을 보호 부품에 통합하여 안전성과 미관을 모두 고려했습니다.
OP20 유압 고정구 소개
처리 지침:
1. φ165 내부 보어를 기본 구멍으로 하고, D 기준을 기본 평면으로 하고, 두 장착 구멍의 보스의 외부 호를 각도 한계로 합니다.
2. 공작기계 M의 명령으로 프레싱 플레이트의 풀림 및 프레싱 동작을 제어하여 장착 구멍 보스의 상부 평면, 8-φ17 장착 구멍 및 구멍의 양쪽 끝에 대한 모따기 가공을 완료합니다.
3. 고정구는 위치 결정, 자동 클램핑, 기밀성 감지, 자동 풀림, 자동 배출, 자동 칩 세척 및 위치 결정 기준면의 자동 세척 기능을 갖추고 있습니다.
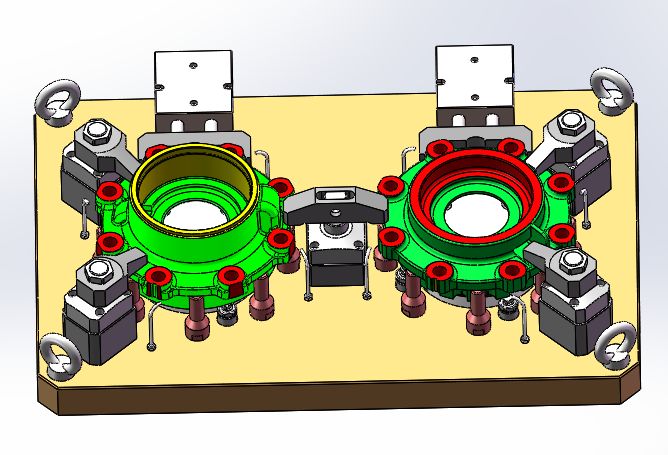
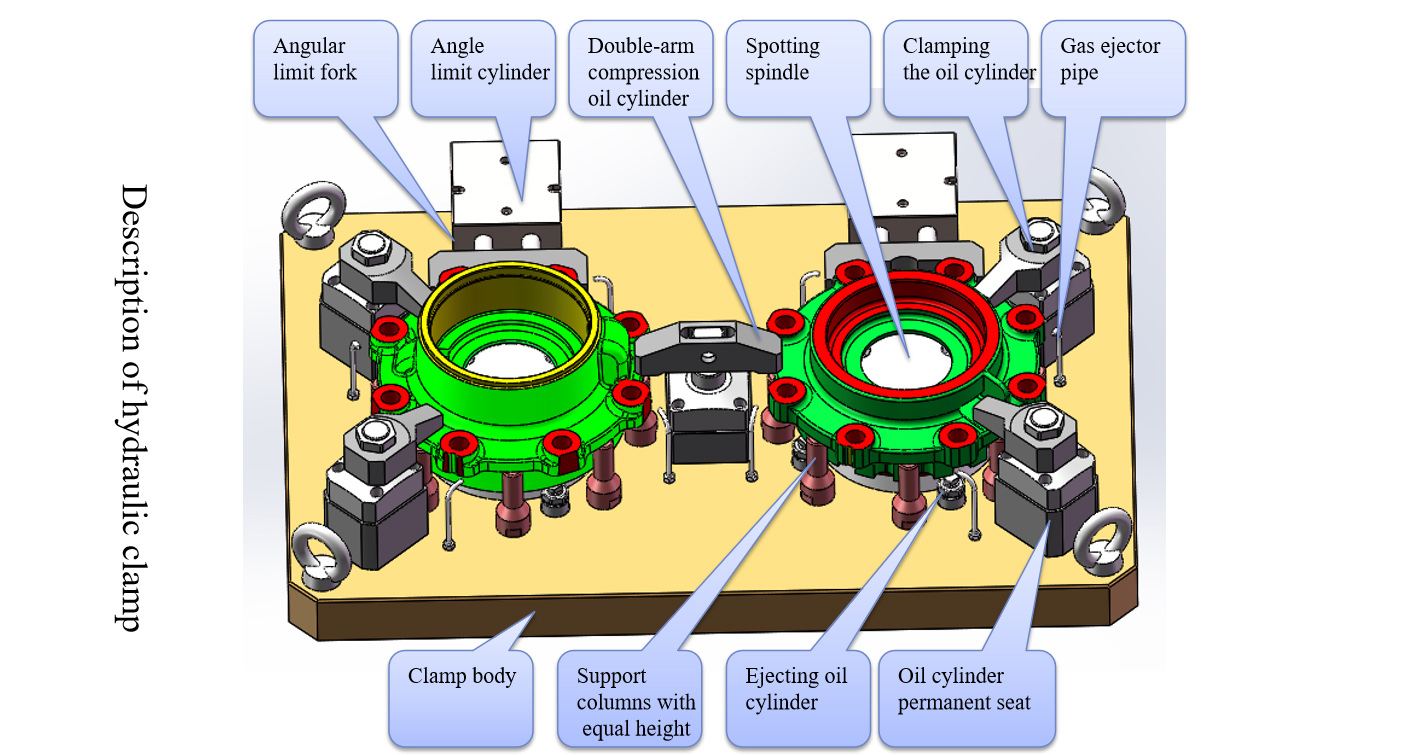
생산 라인에 필요한 장비
1. 생산라인 장비 클램프는 자동 클램핑 및 풀림 기능을 가지고 있으며, 조작기 시스템의 신호 제어에 따라 자동 클램핑 및 풀림 기능을 실현하여 로딩 및 블랭킹 동작과 협력합니다.
2. 스카이라이트 위치 또는 자동문 모듈은 생산라인 장비의 금속판에 예약하여 당사의 전기 제어 신호 및 조작기 통신과 조정해야 합니다.
3. 생산라인 장비는 중량 커넥터(또는 항공 플러그)의 연결 방식을 통해 조작기와 통신합니다.
4. 생산라인 장비에는 조작기 턱 동작의 안전 범위보다 큰 내부(간섭) 공간이 있습니다.
5. 생산 라인 장비는 클램프 위치 결정면에 잔류 철 조각이 없도록 해야 합니다. 필요한 경우, 공기 송풍량을 늘려 세척해야 합니다(세척 시 척을 회전시켜야 함).
6. 생산 라인 장비는 칩 브레이킹 성능이 우수합니다. 필요한 경우, 당사의 보조 고압 칩 브레이킹 장치를 추가 설치해야 합니다.
7. 생산라인 장비가 공작기계 스핀들의 정확한 정지를 요구하는 경우, 이 기능을 추가하고 해당 전기 신호를 제공합니다.
수직선반 VTC-W9035 소개
VTC-W9035 NC 수직 선반은 기어 블랭크, 플랜지, 특수 형상 쉘과 같은 회전 부품 가공에 적합하며, 특히 디스크, 허브, 브레이크 디스크, 펌프 본체, 밸브 본체, 쉘과 같은 부품의 정밀하고 노동력 절감 및 효율적인 선삭 가공에 적합합니다. 이 공작기계는 우수한 전체 강성, 높은 정밀도, 단위 시간당 높은 금속 제거율, 우수한 정확도 유지력, 높은 신뢰성, 간편한 유지보수 등의 장점을 제공하며, 광범위한 응용 분야를 제공합니다. 라인 생산, 높은 효율성 및 낮은 비용.
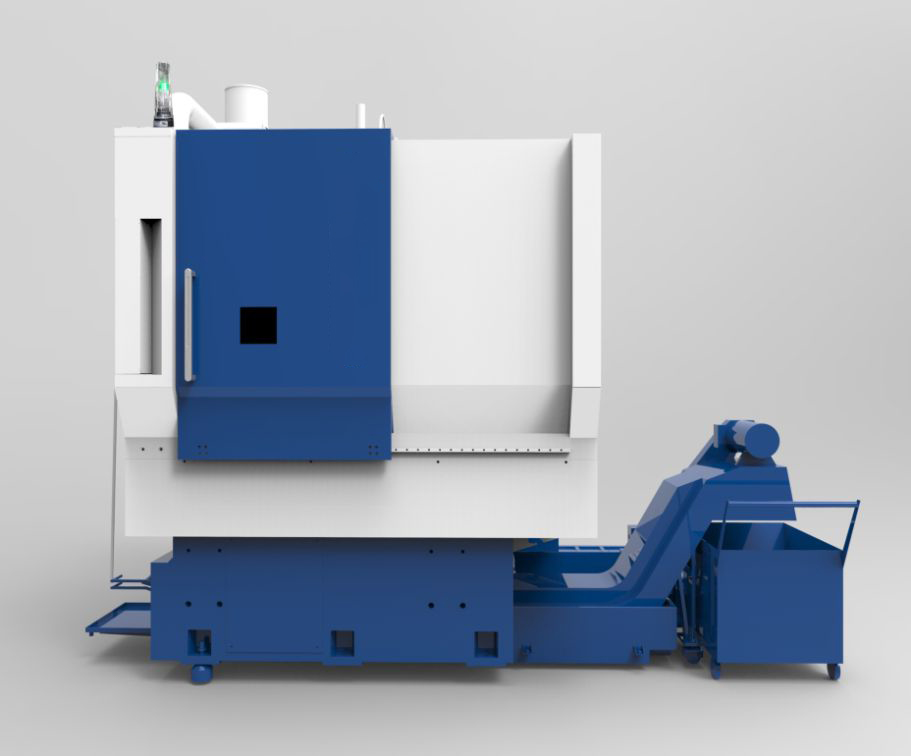
모델 유형 | VTC-W9035 |
베드 바디의 최대 회전 직경 | Φ900mm |
슬라이딩 플레이트의 최대 회전 직경 | Φ590mm |
공작물의 최대 선삭 직경 | Φ850mm |
공작물의 최대 회전 길이 | 700mm |
스핀들의 속도 범위 | 20-900rpm |
체계 | 파낙 0i - TF |
X/Z축의 최대 스트로크 | 600/800mm |
X/Z축의 빠른 이동 속도 | 20/20m/분 |
공작기계의 길이, 폭, 높이 | 3550*2200*3950mm |
프로젝트 | 단위 | 매개변수 | |
처리 범위 | X축 이동 | mm | 1100 |
X축 이동 | mm | 610 | |
X축 이동 | mm | 610 | |
스핀들 코에서 작업대까지의 거리 | mm | 150~760 | |
작업대 | 작업대 크기 | mm | 1200×600 |
작업대의 최대 하중 | kg | 1000 | |
T-그루브(크기×수량×간격) | mm | 18×5×100 | |
급송 | X/Y/Z축의 빠른 이송 속도 | 분당 미터 | 2024년 36월 36일 |
축 | 운전 모드 | 벨트 타입 | |
스핀들 테이퍼 | BT40 | ||
최대 작동 속도 | 분당 회전수 | 8000 | |
전력(정격/최대) | KW | 11/18.5 | |
토크(정격/최대) | 엔·미터 | 52.5/118 | |
정확성 | X/Y/Z 축 위치 정확도(반 폐쇄 루프) | mm | 0.008(전체 길이) |
X/Y/Z 축 반복 정확도(반 폐쇄 루프) | mm | 0.005(전체 길이) | |
공구 매거진 | 유형 | 디스크 | |
공구 매거진 용량 | 24 | ||
최대 도구 크기(전체 공구 직경/빈 인접 공구 직경/길이) | mm | Φ78/Φ150/ 300 | |
최대 도구 무게 | kg | 8 | |
여러 가지 잡다한 | 공기 공급 압력 | 엠파 | 0.65 |
전력 용량 | 케이와이에이 | 25 | |
공작기계 전체 치수(길이×폭×높이) | mm | 2900×2800×3200 | |
공작기계의 무게 | kg | 7000 |
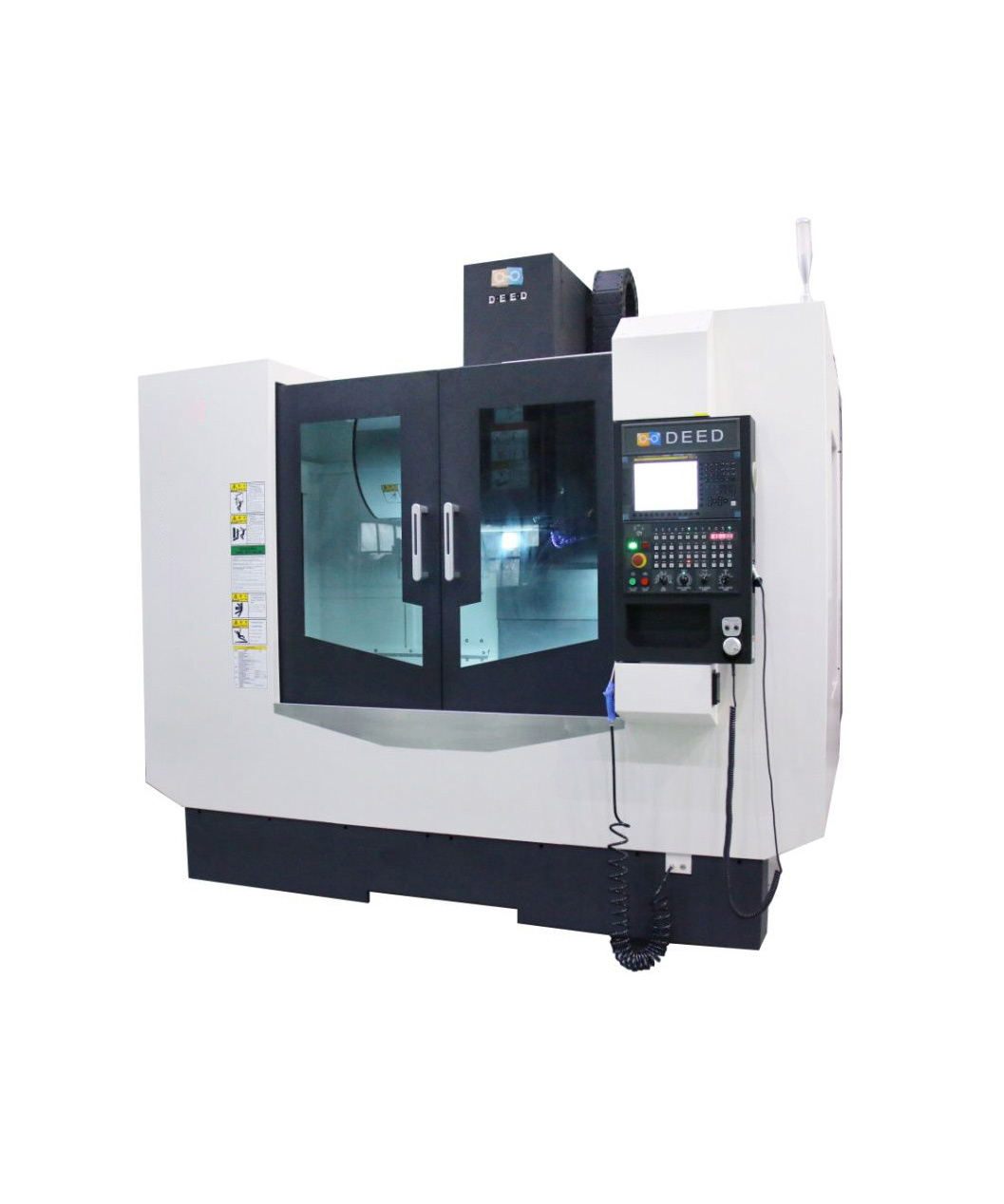